Growing a metal build-up layer on the circuit board tracks and through holes can electroplate the circuit, which is described as PCB Board Circuitry Pattern Electroplating:
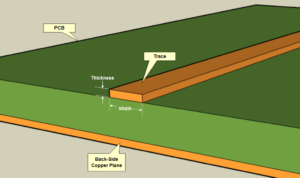
Growing a metal build-up layer on the circuit board tracks and through holes can electroplate the circuit, which is described as PCB Board Circuitry Pattern Electroplating:
In this process, only the places where the circuit patterns and through holes are designed accept the generation of the copper layer and the metal plating of the etching resist. During the printed circuit board electroplating process, the increased width on each side of the circuit and the solder pad is roughly equivalent to the increased thickness of the electroplated surface. Therefore, it is necessary to leave a margin on the original film.
In circuit electroplating, most of the copper surface must be masked by resist, and electroplating is only performed where there are circuit patterns such as circuits and solder pads.
Since the surface area that needs to be plated is reduced, the required power supply current capacity is usually greatly reduced,
In addition, when using contrast reversal photopolymer dry film plating resist (the most commonly used type), the negative film can be made with a relatively inexpensive laser printer or drawing pen.
The copper consumption of the anode in the line electroplating is less, and the copper that needs to be removed during the etching process is also less, so the analysis and maintenance costs of the electrolytic cell are reduced.
The disadvantage of this technique is that the circuit pattern needs to be plated with tin/lead or an electrophoretic resist material before etching, and it is removed before the solder resist is applied. This adds complexity and an additional set of wet chemical solution treatment processes.