There are many conventional methods for PCB Board Thermal Design, such as: hot spot dispersion; the device with the largest heat generation is placed at the optimal position for heat dissipation; the high heat dissipation device should minimize the thermal resistance between them when connected to the substrate; each layer of the PCB It is necessary to lay a large amount of copper and through holes. It is critical to PCB board thermal design in the process of PCB reverse engineering.
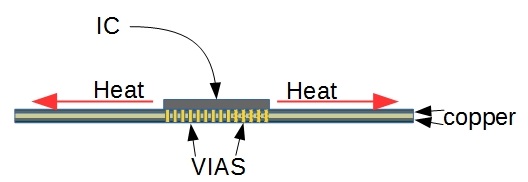
With the deployment of LTE wireless networks, the downlink data rate has reached and exceeded 1 Gbps. To handle such a high data rate, the data terminal must have high data processing capability and inevitably bring about an increase in power consumption. And some of the products we are developing have had hot problems. There are several prototypes that have crashed even in a few minutes during large-speed data transmission.
The root cause of these problems is heat, and PCB board thermal design has become a problem. A challenge for card terminals. An example of Apple’s iPAD product, a large number of users feedback that their products have problems in a higher environment, which reflects the importance of PCB board thermal design for end products. Power consumption has become a key issue for engineers to seriously consider in the early stages of PCB board design.
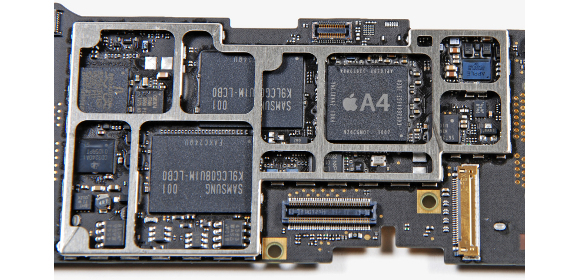
The heat source devices of the terminal platform mainly include baseband chips, radio frequency chips, power amplifiers, power management chips, etc. The power consumption of these devices can be found in the datasheet given by the manufacturer, and some can not be found, and cannot be found from the datasheet. The heat source device of the power consumption data needs to be estimated based on the test data of experience or similar projects, and the relevant data can be obtained directly from the platform provider. Below Table shows the power consumption evaluation results of the main thermal power devices of a project.
AWT6241 1187 mW
RTR6500 706mW
QSD8650 1180mW
PM7540 330mW
ZI1138 444mW
DC-DC 100mW
From the data in above Table , we can see that the power consumption of a data card is close to 4W. In order to dissipate such a large amount of heat in the U disk-sized structural parts, the thermal design of the PCB board can be said to have become a product. A critical design consideration for reliable work.